Getting Welding Quality: Introducing the Secrets of WPS Execution and Optimization
In the realm of welding, attaining excellence is a pursuit that rests on the precise execution and optimization of Welding Procedure Requirements (WPS) These foundational records act as the backbone of welding operations, determining the procedures and specifications needed for creating high-quality welds continually. However, the keys to unlocking the full capacity of WPS lie not just in understanding its value but likewise in mastering the ins and outs of its application and optimization. By diving into the crucial elements, methods, obstacles, and finest techniques connected with WPS, a world of welding quality waits for those who want to explore its depths.
Value of WPS in Welding
The Significance of Welding Procedure Requirements (WPS) in the welding sector can not be overemphasized, working as the backbone for making sure uniformity, high quality, and security in welding procedures. A WPS provides detailed guidelines on exactly how welding is to be lugged out, including crucial variables such as products, welding processes, joint design, filler steels, interpass and preheat temperatures, welding currents, voltages, travel rates, and more. By adhering to a distinct WPS, welders can keep uniformity in their work, bring about consistent weld quality across different projects.
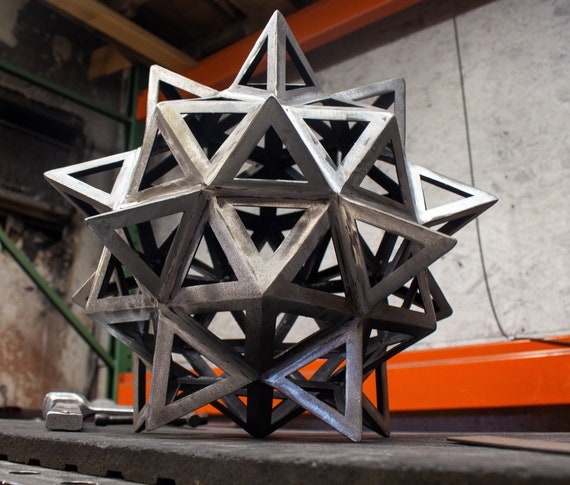
Crucial Element of WPS
Going over the integral components of a welding treatment specification (WPS) is important for understanding its duty in welding operations. A thorough WPS includes numerous crucial aspects that lead welders in achieving quality and uniformity in their job. One important facet of a WPS is the welding procedure requirements, which lays out the details welding procedures to be used, such as gas tungsten arc welding (GTAW) or secured metal arc welding (SMAW) In addition, the WPS consists of details on the welding products, such as the kind and specifications of the base metal and filler metal to be used. The WPS additionally specifies vital variables like welding specifications, interpass and preheat temperature requirements, and post-weld warmth therapy procedures. Furthermore, it consists of details on joint style, fit-up, and any unique techniques or safety measures needed for the welding procedure. By incorporating these crucial elements into the WPS, welding treatments can be standard, guaranteeing high quality, effectiveness, and security in welding procedures.
Techniques for WPS Optimization
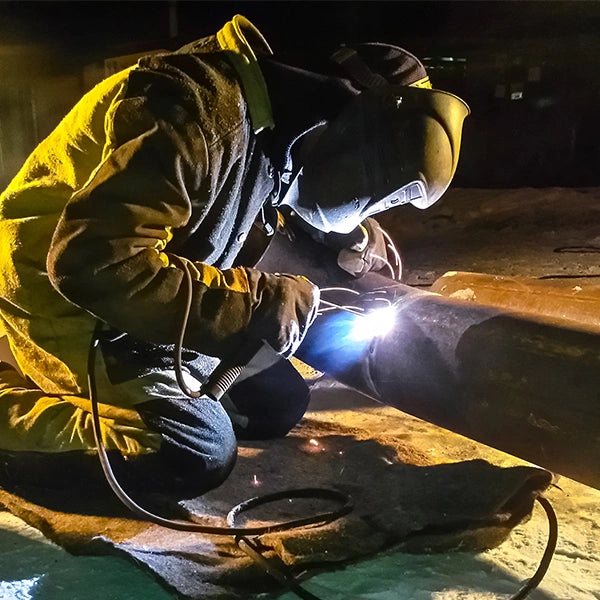
Second of all, training and qualification of welding workers according to the certain demands of the WPS is vital. Providing comprehensive training programs and making sure that welders are licensed to execute procedures laid out in the WPS can result in higher quality welds and reduced rework.
In addition, leveraging technology such as welding software application and monitoring systems can assist in enhancing WPS. These tools can aid in tracking variables, making certain criteria are within specified restrictions, and offering real-time comments to welders, allowing them to make immediate adjustments for boosted weld top quality.
Common Challenges and Solutions
Facing barriers in applying the techniques for WPS optimization can impede welding procedures' effectiveness and quality. One common obstacle is poor training or understanding of the welding treatment specs (WPS) among the welding team.
Another difficulty is the absence of proper documentation and record-keeping, which is essential for WPS optimization. Without clear documents of welding specifications, products used, and inspection outcomes, it becomes challenging to recognize areas for improvement and make certain consistency in welding procedures. Executing a durable documents system, such as electronic welding management software application, can aid improve record-keeping and promote information evaluation for continuous renovation.
Additionally, irregular welding equipment calibration and upkeep can posture a considerable challenge to WPS optimization. Normal equipment checks, calibration, and upkeep schedules must be abided by strictly to guarantee that welding parameters are properly controlled and kept within the specified resistances (welding WPS). By addressing these typical obstacles with positive solutions, welding operations can boost efficiency, high quality, and total welding excellence
Finest Practices for WPS Execution
To make sure effective WPS execution in welding operations, adherence to industry requirements and thorough focus to information are extremely important. When initiating WPS application, it is crucial to start by extensively comprehending the specific welding requirements of the task. This entails a detailed testimonial of the welding procedure specifications, materials to be welded, and the ecological conditions in which the welding will certainly happen.
Once the demands are clear, the following action is to select the suitable welding procedure that lines up with these requirements. This includes getting in touch with the pertinent codes and criteria, such as those given by the American Welding Culture (AWS) or the International Company for Standardization (ISO), to ensure compliance and quality.
Moreover, recording the whole WPS implementation process is essential for traceability and quality control. Comprehensive records must be maintained regarding welding criteria, product prep work, preheat and interpass temperatures, welding consumables used, and any deviations from the original procedure. directory Routine audits and evaluations of the WPS can aid recognize areas for renovation and make certain recurring optimization of the welding procedure.

Final Thought
To conclude, the application and optimization of Welding Treatment Specs (WPS) is crucial for attaining welding excellence. By recognizing Bonuses the key aspects of WPS, implementing reliable techniques for optimization, resolving typical obstacles, and adhering to best techniques, welders can guarantee high-grade welds and risk-free working problems. It is important for specialists in the welding industry to focus on the appropriate execution of WPS to improve general welding efficiency and attain desired results.
The Relevance of Welding Procedure Requirements (WPS) in the welding sector can not be overemphasized, serving as the foundation for guaranteeing uniformity, top quality, and safety in welding procedures. A WPS gives detailed directions on exactly how welding is to be lugged out, including necessary variables such as products, welding processes, joint layout, filler metals, interpass and preheat temperature levels, welding currents, voltages, travel speeds, and a lot more. One crucial aspect of a WPS is the welding process requirements, which describes the specific welding processes to be utilized, such as gas tungsten arc welding (GTAW) or secured steel click for more info arc welding (SMAW) By incorporating these essential aspects right into the WPS, welding procedures can be standard, making certain quality, efficiency, and safety in welding procedures.
It is essential for professionals in the welding market to prioritize the proper implementation of WPS to enhance general welding efficiency and accomplish wanted end results.
Comments on “Understanding Welding WPS: Comprehensive Overview for Welders”